IMTS-Gear Generation
See the latest gear technology at IMTS 2024.
Posted: August 1, 2024
High-precision Gear Cutting of an E-car Rotor Shaft in a Fast Cycle
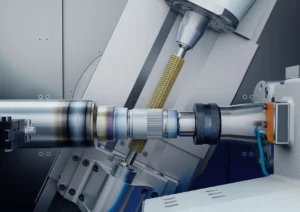
Machining the teeth of a rotor shaft for electric cars has demanding machining requirements. Very few other applications place such high demands as transmission components. The very quiet motor requires the highest surface finishes so that disturbing running noises do not occur. In addition, the number of units in e-mobility is greatly increasing, which is an additional challenge for the mechanical engineering involved. What is needed, therefore, are process-reliable solutions for cost-effective rotor shaft production. EMAG Koepfer’s (Farmington Hills, MI) HLC 150 H gear hobbing machine demonstrates how this can work, ensuring new productivity in this gear sector. EMAG Koepfer will be in Booth N-237047.
The fact that electric cars don’t have any transmissions (apart from the sometimes-indispensable differential) is just a legend — but one that persists quite stubbornly in the public eye. It assumes that the electric motor does not require any gear ratio given its stable torque. In practice, however, it is usually the case that a so-called 1-speed gearbox is used, which helps reduce the speed of the electric motor by a certain factor. As a result, there are numerous gearing elements on components such as the drive shaft, rotor shaft or axle drive, and their component quality must be exceptional so that, for example, there are no loud running noises — these would be audible given the quiet electric motor.
In this context, the technology of EMAG Koepfer is grabbing the attention of production planners. For many years, the specialists have been developing highly versatile mechanical engineering solutions for machining a huge range of workpieces, from gear shafts to steering pinions and worm gears to planetary gears — an ideal experience base for providing highly efficient solutions for the gear cutting of rotor shafts as well. The HLC 150 H gear hobbing machine is one of the focal points here, offering a high level of productivity for components with a maximum length of 500 millimeters and a weight of 10 kilograms. First of all, the milling head ensures this. It is very rigidly suspended and moves completely during machining. The shift axis is made up of the interpolation of two axes. In this way, a large milling head swiveling angle is realized with a large shift path at the same time. As a result, gear hobbing is very smooth and the gear quality is high. The horizontal arrangement of the workpiece also prevents chip clusters from forming. In the end, this technology ensures enormous performance figures in the machining of rotor shafts with cycle times of only 35 seconds at a gear quality of DIN Q7.
Learn more by stopping in at Booth N-237047.
Overall, EMAG Koepfer sees itself well equipped for the growing e-car boom. When it comes to setting up high-volume production in this area, the gear experts offer highly efficient solutions that can be integrated into the manufacturing flow in very different ways. This approach is highly interesting for any production planner — and not just with a view to the rotor shaft.
Gears and Gear Racks Made from Polyamide
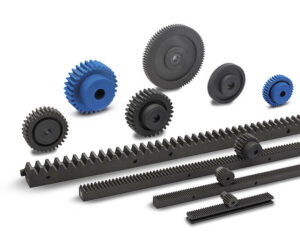
Gears and gear racks used for transmitting torque and forces within gearboxes are typically made of hardened steel. For many other uses and applications, gears and racks made from plastic are the better choice. These generally require no lubrication and are lighter, quieter, less expensive, and more resistant to corrosion than metal gears. This is why J.W. Winco, Inc. (New Berlin, WI) is expanding its range with polyamide gears and racks that can transmit high forces and torques. J.W. Winco will be in Booth W-432287.
Gears and racks made from polyamide are preferred in mechanisms that must transmit high torques at low speeds. This includes packaging machines, chemical and pharmaceutical manufacturers, as well as food production. The components are combined to convert rotational movements into linear or vice versa. Synchronous, symmetrical, or even proportional movements can be easily achieved when used with clamping jaws, grippers or assemblies.
Standard parts specialist JW Winco has considered the basic principles of gearing and introduced the spur gears EN 7802 and gear racks EN 7822 made from strong and long-lasting polyamide. Due to their low friction coefficients, these require no lubrication and are made of FDA-compliant glass fiber-reinforced plastic suitable for food processing applications. The components are also available in gray or blue for better visual detectability.
The polyamide gears and racks from JW Winco are designed for temperatures up to 248 °F (120 °C) and for contact with aggressive media such as acids, gases and saltwater. The gears and racks are designed as an involute gear with a 20° angle, and the design structure helps to reduce torque variation and allow for greater assembly flexibility.
JW Winco offers spur gears EN 7802 designed in module sizes from 0.5 to 3. The polyamide gear racks EN 7822 can be ordered with module sizes from 1 to 3 and feature a steel core to prevent deformation.