IMTS-Metal Removal
A variety of metal removal machines will be displayed in Chicago at IMTS.
Posted: August 1, 2024
Advanced Machine & Engineering and Hennig, Inc. to Exhibit Together
Two Goellner family companies, Advanced Machine & Engineering (AME) (Rockford, IL) and Hennig, Inc., will be exhibiting together at IMTS for the first time. Both companies will be showcasing a wide range of leading-edge technologies designed to keep machine tools operating safely at maximum efficiency and accuracy.
AME and Hennig, Inc. will be exhibiting in Booth S-338460. Technologies on display in the booth will include:
- AMROK tombstones and fixture plates, plus a wide range of modular workholding solutions .
- Multiple Hennig chip conveyors.
- Hennig high-pressure coolant systems.
- Trinity Automation AX2 Automated Pallet System connected to a vertical machining center .
- Hennig protection solutions including machine protection, pit covers, roof bellows, telescopic steel covers and cable carriers.
- OTT-JAKOB tool clamping systems.
“We’re thrilled to have both companies exhibiting together at IMTS,” said Nick Goellner, vice president of sales & marketing for AME and Hennig, Inc. “Booth S-338460 is a must see for all visitors to IMTS 2024. Whether you have one machine tool or a thousand machine tools, we will have a range of technologies on display and application engineering experts on hand to help you improve performance, productivity and profitability.”
GF Machining Solutions to Highlight Innovations From System 3R
A company with innovation at its core, GF Machining Solutions (Lincolnshire, IL) will feature some of the latest advancements in tooling, automation and software from System 3R in Booth S-339458. Regardless of machine make or model, System 3R helps boost manufacturing output through smart productivity solutions. System 3R is the leading supplier of productivity-enhancing tools and knowledge for the manufacturing industry.
The company’s modular tooling reference system minimizes setup times, while maximizing spindle uptime for high output. Shops increase profitability by working smarter, not harder, with tooling systems for EDM and electrode manufacturing, parts production and powder compacting applications.
For 24/7 production, System 3R Automation offers scalable automation solutions. Among those are the company’s WorkPal 1, WorkPartner 1+, Transformer WorkMaster and Transformer 6-axis robot, all of which shorten lead times and maximize ROI.
On the software side, System 3R’s solutions are user friendly. Necessary data are entered quickly and in a structured manner, giving users a quick, precise overview of their entire process chain. In addition to simpler, safer preparation of automatic cells, the various software solutions make information about workpieces, magazine positions, offset values and NC programs always readily available.
The company’s extensive software portfolio packages include WorkShopManager, CellManager, EasyCellManager, CellManager Light and BatchBuilder. For seamless integration of all shop operations, WorkShopManager provides a quick and accurate overview of the complete process chain and management of the entire automation system.
CellManager is for one or up to 12 machines in a cell and supports different types of machines such as milling, sinker and wire EDM, laser, coordinate measuring machines (CMM) and cleaning. EasyCellManager applies to one to four machines, supporting milling and laser texturing only. CellManager Light is for robot less systems encompassing one or as many as 12 machines in a cell with different types of machines such as milling, wire and sinker EDM, laser and CMM.
As an entry level software, BatchBuilder allows users to create job batches to run in their robot cells that have various types of milling, sinker and wire EDM, laser and CMM machines. Key benefits of the software include full process optimization, ease of use and added scheduling flexibility with process chain monitoring.
GROB Systems to Demonstrate Challenging, Automated 5-Axis Machining Applications
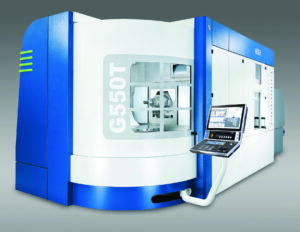
GROB Systems, Inc., (Bluffton, OH) a global leader in the development of manufacturing systems and machine tools, will demonstrate a range of 5-axis machining applications at Booth W-431400 (YG-1 Tool Co. booth), and at Booth W-431436 (Allied Machine & Engineering booth).
GROB machining centers, which are compatible with Industry 4.0 principles, are made in the U.S.A. at the GROB Systems full production facility in Ohio and often include advanced automation solutions for dramatically increased productivity. Having the machining center and automation come from the same builder offers customers streamlined service and support to keep the entire cell running at long-term high efficiency. GROB machines feature a unique machine concept including a horizontal spindle position that permits the longest possible Z-travel path and optimum chip fall.
At Booth W-431400 (YG-1 Tool Co. booth):
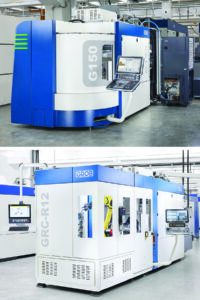
The GROB G150 5-Axis Universal Machining Center integrated with the GRC-R12 Robot Cell will be under power. The G150 provides high precision, complex machining in a compact size with a smaller work envelope. Featuring direct and absolute position encoders in all axes and an innovative machine cooling process, the machining center provides exceptional contouring accuracy. Pairing the G150 with the compact GRC-R12 Robot Cell increases productivity even further by offering a flexible, customizable and affordable automation solution. The cell has a 6-Axis FANUC M-10iD/12 Robot with 4.7′ (1,441 mm) reach, capable of handling a maximum load of 26.5 lbs. (12 kg). The GRC-R12 features a pneumatic single- or double-gripper system. The drawer feed system can have up to six drawers that can be unloaded and reloaded while the robot cell and machining center are in operation. Multiple machining demonstrations will be held throughout each day.
At Booth W-431436 (Allied Machine & Engineering booth):
The GROB G550T 5-Axis Mill/Turn Universal Machining Center is capable of machining a part by milling and turning in a single setup, saving time, costs and floor space. The machine is equipped with a Siemens 840D SL control, 14,500 rpm spindle, and an HSK-T100 tool interface. For maximum stability and machining performance, the G550T features a powerful mill-turn table with t-slots arranged in a star shape. Three linear and two rotary axes permit five-sided machining, as well as 5-axis simultaneous interpolation, with a swivel range of 230° in the A-axis and 360° in the B-axis. The drive design is based on two symmetrically located ball screws, weight compensation in the Y-axis, and wear-free torque motors in the A and B axes.
Attendees will see demonstrations including an aerospace hydraulic manifold milled from 4140 steel supported by hyperMILL CAM programming from OPEN MIND Technologies.
High-precision Technology and Turnkey Solutions
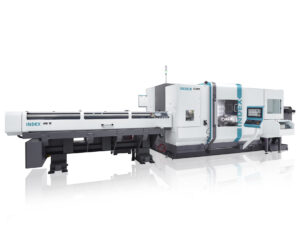
INDEX (Noblesville, IN) will demonstrate its full range of high-precision machining solutions at IMTS, which will include the North American debut of its C200 FANUC, a cost-effective new variant of its highly successful production machining center. The company will also showcase the INDEX iXperience, its comprehensive portfolio of value-added services that provide manufacturers with an optimized solution, from acquisition and installation of a single machine to development and delivery of a turnkey production system. INDEX will be in Booth S-339119.
The C200 FANUC merges the innovative design and high performance of INDEX’s successful production
turning center with a FANUC control. Powerful twin spindles achieve rapid material removal while the patented SingleSlide guide system offers an incredibly fast dynamic response by providing two degrees of movement in one plane. The machine’s inclusion of a third turret enables dramatic productivity gains, as it can quickly move between spindles for high flexibility and cycle time minimization.
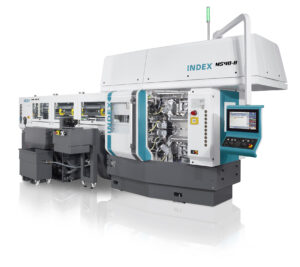
With eight motorized spindles, the MS40-8 CNC multi-spindle allows for extremely short cycle times on both complex and simple parts. The machine is available with dual synchronized spindles and can be operated in a double four-spindle mode to produce two complete parts with every full rotation of the spindle drum. The machine can be configured with up to 18 CNC slides, as well as additional Y axes, to perform a diverse range of processes. All of the machine’s motorized spindles are fluid-cooled and can operate independently of the other seven, allowing each to apply cutting data optimized to the process being performed.
Able to switch between sliding- and fixed-headstock operation in minutes, the TNL20 provides a powerful, flexible solution for shops producing parts suited to Swiss-type machining. With a rigid, vibration-damping bed, the TNL20 maintains exceptional accuracy while also allowing up to four tools to be put in the cut simultaneously. With two turrets and the use of double and triple holders, the machine can accommodate up to 58 tools to flexibly tackle a wide range of complex small parts.
Designed to fully machine even the most complex parts in a single setup, the G220 turn mill combines powerful twin spindles, two turrets, robust 5-axis milling capabilities and a capacity to hold up to 169 tools. The machine offers high dynamics and generously dimensioned linear guides in the X and Z axes, allowing it to achieve optimal cycle times for parts with numerous, varied features and specification requiring tight tolerances.
In addition to seeing cutting demonstrations on world-class machines, visitors to INDEX’s booth will have the opportunity to learn about the INDEX iXperience. This term encompasses the total company approach that INDEX has developed to efficiently and effectively provide whatever level of solution a manufacturer requires.
It includes close coordination between the sales, proposals, project management, applications, service and spare parts teams to ensure a comprehensive and ongoing solution to a customer’s needs.
Drilling Machine used in Helicopter Manufacturing
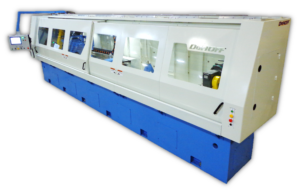
The DeHoff 25108 (a product of Kays Engineering, Inc. in Marshall, Mo.) is a BTA drilling machine used to manufacture helicopter tail rotor drive shafts. The shaft begins as a solid piece of high-strength alloy steel and is drilled in a single pass using the DeHoff machine. This results in a significant weight reduction for the finished drive shaft. The company will be in Booth S-338373.
The DeHoff 25108 has a BTA drilling diameter capacity of 2.5” (63.5 mm) and a maximum drilling depth of 108” (2,743 mm). It features a 20 hp AC spindle motor and four-speed gearbox to provide versatile drilling performance. The workpiece is counter-rotated in the opposite direction of the drill rotation, which improves the accuracy of the drilled hole.
Precision Machining Offers Repeatability and Versatility
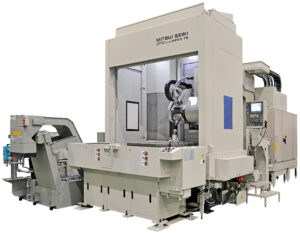
Mitsui Seiki (Franklin Lakes, NJ) is bringing three of its most versatile and accurate machines to Booth S-338700. What’s more, Mitsui Seiki Regional Sales Manager Tyler Bonde will reinforce the Mitsui Seiki technology in the company’s booth by teaching attendees how to achieve repeatable accuracy in his conference talk “Precision Repeatability: How to Make Great Parts Over and Over and Over Again” at 11 a.m. on Wednesday, Sept. 11. This interactive discussion promises to teach attendees the key elements that go into achieving precision repeatability, how to set up for success with the equipment users already have, and how to ensure they get the necessary machine tool needed to achieve their goals.
The machines outlined below, when used in tandem or on their own, enable users to produce highly accurate parts again and again:
-
Booth S-338700: Vertex 55X III can perform multiple functions in one machine, making it ideally suited for aerospace and mold and die work. Vertex 55X III: The ultra-high precision Vertex 55X III can perform multiple functions in one machine, making it ideally suited for aerospace and mold and die work. The 55X is designed for versatility and precision and can be adapted to integrate seamlessly into any machining cell. To demonstrate this, the 55X at IMTS will showcase a field retrofittable pallet system with shared tool capacity, and a total of 12 pallets and 140 tools.
- HU100-TS 5-Axis Tilt Spindle Machining Center: The HU100-TS ’s powerful linear and rotary axes are configured with a high torque spindle making it ideal for machining complex parts with precision and consistency. The updated line provides exceptional rigidity and accuracy to profitably mill materials such as titanium, Inconel, stainless steel, and challenging alloys common in aerospace, power generation, defense and other ultra precision, high-value applications.
- J350G Jig Grinder: The J350G offers a combination of application flexibility, accuracy, reliability and operator-friendly operation. The grinding infeed stroke is the largest available among all machines in its class. With a U-axis range of -3 mm-to- +50 mm relative to the spindle center, this solution provides the versatility to grind small and large diameter holes, as well as free-form complex features, using a single wheel in a continuous, automatic mode.
New Generation Lathe and Turning Center to be Demonstrated
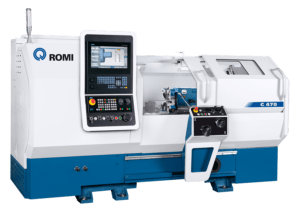
Romi BW Machine Tools Ltd. (Erlanger, KY) will feature a New Generation C 470 CNC lathe and a New Generation GL 300S horizontal turning center. Romi will be in Booth S-338876.
The New Generation C 470 is a teach lathe with an 18.5″ (470 mm) swing over bed, a 4,000 rpm 12.5 hp main motor, and 39.37″ (1,000 mm) between centers. It is equipped with the Romi Manual Machining Package (RMMP), which allows simple operations to be completed without any programming. It is as simple to use as a manual lathe but with a CNC lathe’s added capability and productivity.
Using the RMMP, an operator can machine parts manually using the handwheels or automatically using a joystick and start cycle. The operator can also fill in the fields on the CNC screen, indicating spindle speed, feeds, cutting depth, coordinates, and angles, and start the machining with the cycle start button.
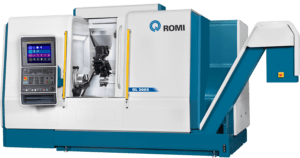
All key components of Romi C Series lathes, including the robust monoblock bed, are designed and built in-house for complete control and assurance of manufacturing quality. For example, the bed features a robust structure supported by cast-iron columns and is internally ribbed to absorb vibrations during machining, ensuring unparalleled precision and stability in every operation.
It is equipped with a Siemens Sinumerik 828D CNC. This high-performance CNC features a 15” color LCD touchscreen and provides excellent conversational programming, operation, and machining simulation resources.
Romi’s New Generation GL 300S horizontal turning center is equipped with a sub-spindle and a Y-axis for off-center milling. With a maximum cutting diameter of 11.8″ (300 mm) and Z-travel of 23.6″ (600 mm), it is designed for turning, milling, and drilling operations in high-production environments. The GL 300S features high power torque and feed force and is built with a robust Romi-made monoblock base for ultimate rigidity and precision. The machine weighs 11,464 lbs. (5,200 kg).
The horizontal turning center also comes equipped with thermal compensation with sensors to maintain stable, dimensional results even during long working periods. What’s more, durable roller ways on all axes ensure high rigidity and longevity. The 12-station BMT55 turret with driven tools and a Y-axis further enhances its versatility and durability. The built-in spindle and sub-spindle motors, with chiller incorporated and direct drive servo motors, produce high response speed and accuracy and require less maintenance.
The CNC control is a Fanuc 32iB with a 19″ LCD touchscreen, which produces faster, more accurate performance for turning applications with separate areas on the main screen for planning, machining, improvements and utilities.
Expansive Range of Deep Hole Drilling Solutions
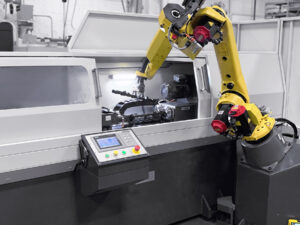
UNISIG Deep Hole Drilling Systems (Menomonee Falls, WI) will showcase its comprehensive portfolio of deep hole drilling solutions in Booth S-339159. Manufacturers in industries ranging from aerospace, automotive, medical and mold making to energy, firearms and defense can learn how to achieve a competitive advantage with UNISIG’s 50-year leadership in deep hole drilling technology and automation paired with unmatched engineering, sales and service support.
UNISIG offers an entire deep hole drilling system — machines, tooling and automation — that covers the full range of deep hole drilling applications. Engineered and manufactured in the United States for a global customer base, UNISIG machines are used in applications that can vary from drilling holes less than 0.040” in diameter for titanium medical components to 20” diameter holes over 30’ deep in massive high-strength forgings. UNISIG’s USC-M drilling and milling centers combine 5-axis CNC milling and deep hole drilling in one machine platform for maximum versatility with fewer setups and reduced part handling.
Productivity and cost efficiency are maximized with UNISIG’s extensive experience in designing and integrating a variety of standard and specialized automation solutions into its deep hole drilling machines that include pallet changers, robotics, programmable smart conveyors, heavy bar loaders and bulk feeders.
In addition to discovering the company’s wide range of deep hole drilling technology, visitors will be able to view an assortment of parts from medical to aerospace components that demonstrate the breadth and depth of UNISIG’s deep hole drilling capabilities. UNISIG personnel will also be available to discuss machine tooling and automation solutions for those customers with unique manufacturing needs and challenges and detail the company’s dedication to comprehensive training and support.