IMTS 2024-Tooling & Workholding
The lateset technology in tooling and workholding will be on display at IMTS 2024.
Posted: August 2, 2024
Fixtureworks to Feature Expanded and Extensive Product Line
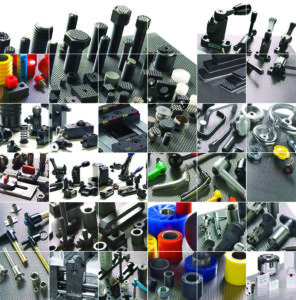
Fixtureworks® (Fraser, MI), a leading supplier of clamps, fixturing accessories, machine tool and material handling products, will showcase its entire high-quality product line in Booth W-432377.
Fixtureworks will highlight some of the newest additions to its lineup of products, including retractable ball lock fasteners, heavy-duty push lock clamps, flat-style clamping fasteners and a new larger module for the 5-axis modular clamping systems for large workpieces.
Also featured will be myriad workholding products including pneumatic clamps and workholding devices, nutrunner clamps, one-touch fasteners, 5-axis modular clamps, flex locators, and many other fixture clamps and locating system solutions. As well as an extensive selection of machine components including mechanical linear actuators, handles, levers, knobs and grips, hand wheels, cranks, industrial rubber bumpers, stops and wheels. Many new demos will be on display at the booth for a direct hands-on experience of Fixtureworks’ newest products.
Also featured will be Fairlane® Products line of workholding and positioning products that help extend the life of expensive jigs, fixtures; bumpers and rollers that come in a wide variety of styles to help guard, align and protect workpieces; and clamping mechanism including grippers, rest pads, and Swivots® swivel/pivoting positioning components.
Enhanced Digital Readout Module for Precision Boring Applications
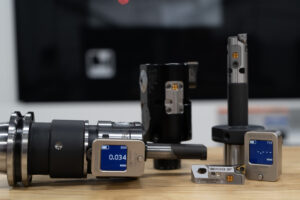
Allied Machine and Engineering (Dover, OH), a leading manufacturer of hole making and finishing cutting tools for the metal-cutting industry, will showcase the Wohlhaupter 3ETECH+ digital readout module in Booth W-431436.
The 3ETECH+ digital readout module provides improved diameter adjustment accuracy of one micron on Wohlhaupter digital boring tools, making it the ideal choice for holding precision hole tolerances on expensive parts. High-production environments such as aerospace, heavy equipment and automotive greatly benefit from the enhanced digital readout module, which can be used on various Wohlhaupter boring tools including VarioBore versatile boring heads, 420 (410) series boring heads, 465 (464) series balanced boring heads, 538 (537) fine boring cassettes, custom boring solutions and the ES-Bore series of fine boring lay down cartridges.
As many machine shops move away from vernier dial (analog) adjustment because of the ease of use digital readout modules provide, having an external, removable digital module also eliminates the worry of costly digital tooling components being harmed by cutting chips or high-pressure coolant. Wohlhaupter’s proven precision technology has aided in improving boring operations, and the following enhancements of the 3ETECH+ add to the benefits for machine shops:
- Enhanced visibility with backlit OLED display and larger screen.
- Easier charging capabilities with rechargeable battery via USB-C.
- Multiple display color options for optimal visibility in any environment.
- Screen auto-rotate function to match the orientation of display module.
- Toggle between imperial and metric adjustment to accommodate all applications.
New Line of Ultrasonic/Heat-stake Metal Inserts
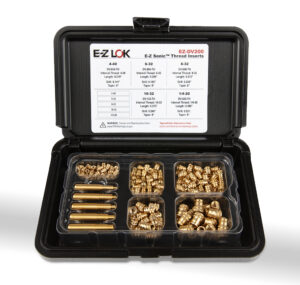
E-Z LOK (Gardena, CA), a leading manufacturer and master distributor of threaded inserts for metal, plastic and wood, will display its products in Booth W-432123. The company will be co-located with its sister company TCI Precision Metals, a leading supplier of metal materials and near-net shapes to machine shops and fabricators. Highlight of the show for E-Z LOK will be its new line of ultrasonic/heat-stake metal inserts and staking tools for plastics, which can be used for OEM builds as well as retrofits and even injection molding over core pins for creation of strong components with higher torque and pullout strength in use.
In addition, the full line of E-Z LOK threaded carbon inserts with factory-applied LOCTITE™ 204 adhesive coating will be displayed. Once installed in a metal substrate for repair or added strength in an OEM application, the adhesive seals against liquids and gases to 6,000 psi and can perform in temperatures up to 300°F. These proprietary inserts were developed by the current owner Ben Belzer’s grandfather for the aerospace industry as an alternative to helical inserts.
A new feature of the E-Z LOK website, www.ezlok.com, is the CAD file, which allows an engineer to incorporate any of the thousands of E-Z LOK inserts into a design. Director of sales and marketing, Kyle Lindsly-Roach and a team of E-Z LOK engineers will attend the show, displaying the full line of E-Z LOK products. Emphasis will be placed on the company’s threaded inserts for metal, wood and plastic. “We are excited to be able to present our portfolio of products to a wide range of customers, including engineers, OEMs and distributors,” said Lindsly-Roach. “We hope to be able to expand our customer base and the industries where our products are, as well as our existing supply chain partners in the OEM, fastener distributor and machine shops.”
Precision Products and Advanced Tool Management Systems
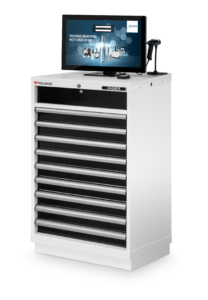
Simplify your manufacturing with HAIMER USA’s (Villa Park, IL) precision products and advanced tool management systems, WinTool and ToolBase. Integrate our high-precision tool holders, shrinking technology, balancing machines, and tool presetters to reduce production costs and boost productivity. Enjoy shorter programming and setup times with organized manufacturing documentation. Customizable ToolBase dispensing systems eliminate outdated demand determination and ordering processes. WinTool ensures continuous data exchange and robust access management, providing complete traceability of your equipment. Pair HAIMER’s precision products with WinTool and ToolBase technology for unparalleled efficiency and reliability. Experience the future of machining with HAIMER – where speed, accuracy, and seamless integration drive optimal performance. Please visit the HAIMER Booth W-431510 to see how all of the HAIMER technology can work together to maximize efficiency in the tool room.
Back Spot Facing Tools
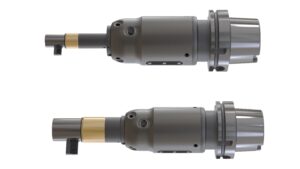
HEULE Precision Tools (Cincinnati, OH) will feature their BSF tooling for automated high-volume back spot facing applications in Booth W-431364. It is ideal for counterbores up to 2.3 x diameter and ranging in size from 6.5 mm to 20.5 mm (0.256” to 0.807”). BSF tooling is available with three activation methods to suit any machining environment, including, (1) CNC machines with through-spindle coolant with at least 300 psi; (2) CNC machines with through-spindle air with at least 60 psi; and (3) a new manual version with easy collar locking /unlocking mechanism. BSF tooling is designed for CNC machining and functions without an anti-rotation device, change of spindle direction, or contact mechanism, allowing components to be spot faced in the same direction as the bore is drilled. This saves the time and cost of turning the workpiece, while allowing the spot facing of difficult to reach areas like casting flanges, and bolt head faces. The simple swing mechanism combined with one of the three activation methods yields optimal cutting performance, resulting in consistent spot facing and fewer scrapped parts. BSF tooling is stocked in the Cincinnati area warehouse for immediate shipment. They are ideal for gear housings, yokes, engine casings, and other parts in a wide range of materials.
The blade expands using centrifugal force when activating the spindle, and retracts from coolant pressure, air pressure, or manually, which moves a piston to depress a pin which retracts the closed blade into the blade housing. The tool works both vertically and horizontally, with replaceable carbide-coated blades for extended tool life. Designed for optimal cutting performance, chip removal, and reliability, the BSF coolant-through tool and blade feature special coolant pipes and chip-guiding geometries that continuously flush the blade window and the blade itself with coolant. This keeps the work area clean and allows for optimal chip removal. All tool components and blades are easy to replace.
Full Line of Innovative Workholding Products and Beer Boots
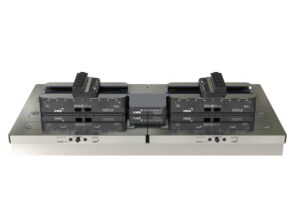
HWR Workholding USA (Noblesville, IN) has announced that it will be bringing its full line
of innovative workholding products to IMTS. Exhibiting at IMTS for the first time, HWR will be highlighting new and existing solutions for both turning and milling applications. Additionally, the booth will feature a RoboJob automation cell demonstrating the ease with which HWR products facilitate process automation.
Visitors to the company’s booth will also have the opportunity to pick up a commemorative beer boot as a German-centric souvenir. Attendees will find HWR in Booth W-431579.
For milling applications, HWR will showcase its SOLIDLine family of zero-point workholding products. The newest of these include SOLIDGrip MAXX and SOLIDBolt FLEXX, both released in 2024. SOLIDGrip MAXX allows users to quickly convert two standard vises into a single large-capacity vise with a maximum clamping range of 800 mm (31.5″), offering a highly secure, cost-effective solution for large-part manufacturers.
Tailored to specific machine makes and models, SOLIDBolt FLEXX simplifies and streamlines the integration of zero-point workholding systems by allowing a zero-point plate to be installed directly to a machine’s table or pallet. It enables fast and easy implementation of vises, risers, chucks, pyramids and other workholding components. SOLIDBolt FLEXX is currently available for the Makino DA300P, Matsuura MAM72 Series, Mazak Variaxis i-300 AWC and YASDA PX30i.
The company will also display its SOLIDPoint mechanical zero-point technology, SOLIDClick 5-axis centering vise for contour clamping, SOLIDGrip centering vise, SOLIDStamp stamping unit and SOLIDClean chip fan.
On the turning side, attendees will see the company’s unique INOLine clamping system. This includes INOFlex four-jaw chucks that use a unique design that allows each set of jaws to operate independently to achieve secure clamping of round, rectangular and asymmetrical parts.
Also on display will be the INOZet pendulum bridges, which empower manufacturers to double the number of jaws on their existing chucks to more evenly distribute clamping force and eliminate part deformation. Attendees will also see INOTop hybrid clamping jaws, which use external pressure to center delicate parts and then clamp them internally to avoid damaging them.
Modular Quick-change Workholding Solutions and Automation Capabilities
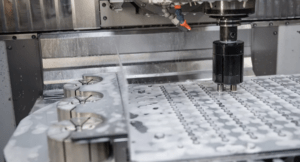
The MT-S Spindle Gripper is pictured.
Jergens Inc. (Cleveland, OH) will present its expanded range of modular quick-change workholding solutions and automation capabilities in Booth W-432154. Featured products will include the company’s range of 5-axis vises and top tooling, cast iron tooling columns, Zero Point System, low profile clamping and Quick-Loc™ pallets.
Additionally, Jergens’ Custom Design & Build (CD&B) capabilities will be presented. Leveraging the company’s experience in engineering and manufacturing quick-change workholding systems, the CD&B initiative focuses on solutions based upon the needs that both the part and the machining platform present. In many cases, the use of standard workholding provides the basis for optimal solutions, shortening the time to market and allowing customers to enhance their manufacturing productivity with efficient quick-change products.
Another key feature for Jergens this year is the company’s growing automation offering for unmanned and lights out manufacturing. That includes combinations of such products as a machine washdown tool, Zero Point System (ZPS), a range of pneumatic and hydraulic devices, and a new spindle gripper for first level automation without a robot. The MT-S Spindle Gripper allows continued machined cycles by picking and placing finished components in a temporary part loading tray located within the machining area. The MT-S is stored in the tool magazine like any tool and engaged at the end of each cycle allowing continuous machining until the part loading tray is full. Advantages of the new gripper are no additional floorspace needed, lower initial investment compared to robotics, and fast training without extensive programing.
The Safer Way to Store Assembled CNC Cutting Tools

The Tool Caddy™ from Kaiser Manufacturing (Carol Stream, IL) is a compact storage solution for assembled CNC tooling. The narrow stainless-steel cart has up to 82 locking, horizontal pockets for all major spindle interfaces. Kaiser Manufacturing will be in Booth W-432141.
The horizontal arrangement of the tool pockets greatly improves machinist safety. Traditional tool racks and carts keep tools in a vertical position with the cutter tip pointing up. This creates a risk of injury for operators when they need to reach over sharp edges to access other tools in the middle or back of the cart.
The Tool Caddy design makes it easy and convenient for the operator to grab each toolholder without any risk of cuts, and it uses only about 4 square feet of floor space. Each tool pocket is slightly angled to safely support the tool while allowing coolant to run off the tool tip and collect in the integrated drip pan. This further improves safety by keeping fluid spills off the shop floor.
Tool Caddy is practical and convenient for tool storage next to the machine, by the pre-setter, or for organizing special tool sets. It is available for CAT 40, CAT 50, HSK 63, HSK 100, BT and Capto tool holders.
New Modular CNC Machine Tending Platform for High-mix, Low-volume Production
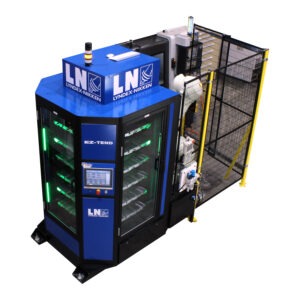
Lyndex-Nikken Inc. (Mundelein, IL), a manufacturer and provider of high-performance machine tool accessories and automation, introduces the EZ-Tend modular CNC machine tending platform that is designed with innovative lean tending in mind for high-mix, low-volume production. Already well known on the machine shop floor for high-performance machine tool accessory solutions that deliver exceptional results, Lyndex-Nikken is now meeting demands of industry with a product line of EZ-Automation solutions for machine shops.
The EZ-Tend is an easy-to-use industrial robotic machine tending platform with compact footprint that is an automation solution within Lyndex-Nikken’s EZ-Automation product line. The EZ-Tend is an off-the-shelf automation platform ideal for first time or entry-level industrial robotic users as well as experienced professionals wanting ease of use and setup of an industrial robot for machine tending.
Leveraging lean manufacturing processes, the EZ-Tend elevates lean manufacturing to new heights by employing industrial robots to perform lean machine tending of CNC machines. Unlike traditional automation solutions, EZ-Tend focuses on simplicity and efficiency without the need to address robot programming or paths.
The core of EZ-Tend’s simplicity lies in its use of a proven lean manufacturing technique: pallet changing. This approach enables the user to standardize on one of three pallet sizes: 6”-x-6”, 6”-x-9”, and 9”-x-20”. This flexibility is achieved through preconfigured drop down options in the HMI easily understood for fast setup, this eliminates the need for complex robot programming.
The EZ-Tend is capable of tending milling centers and turning centers. Its Human Machine Interface (HMI) is designed for simplicity — allowing a non-robot programmer to create a routine using an easy to read and understand menu with just one screen to set up a new program.
The EZ-Automation product line is designed with simplicity in mind, ensuring manufacturers a stress-free entry into Industry 4.0/5.0 and smart factory capabilities. All E-Z Automation products are based on being easy, modular, and scalable automation solutions that will range from machine tending, to machine loading, to work changers, and modular tending platforms. The products offer efficiency and cost-effectiveness providing user-friendly automation solutions, minimizing the need for advanced robotics or automation skills. EZ-Automation products are designed to be seamlessly integrated while controlling costs and easing job complexities for manufacturers.
Hommel + Keller Quick Knurling and Marking Tools Available From Platinum Tooling
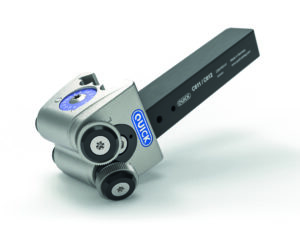
QUICK® knurling and marking tools used in various industries including medical, aerospace, automotive and fitness, will be shown in Booth W-432245. Platinum Tooling Technologies, Inc. (Prospect Heights, IL), the importer and master distributor of live tools, angle heads, marking tools, Swiss tools and multi-spindle tools manufactured by various global suppliers, is now the North American importer of the QUICK knurling and marking tools from Hommel & Keller.
A longtime global leader in high-end knurling and marking tools, Hommel & Keller manufactures the QUICK line with a combination of function and innovation. Quality, precision and stability are the key principals used to make QUICK tools successful. Furthermore, the company prides itself on a rich history of providing customized solutions for its customers.
The QUICK product spectrum offers innovative solutions for diverse knurling technology applications. For both form knurling and cut knurling, QUICK fulfills the most stringent quality standards and masters difficult tasks. Knurling tools are available for use on a wide range of workpiece diameters, including small tools for Swiss type lathes from Ø 1.5 mm.
QUICK marking tools make it possible to mark workpieces in seconds on a variety of surfaces and part geometries. Through single marking segments, the marking text can be individually customized. Tools are available in two diameters for interchangeable lettering, as well as custom logos.
These tools are used whenever absolute precision and first-rate surface quality are needed. Examples include medical and dental instruments, watches, fishing gear, windshield wiper shafts, barbells, screwdriver bits, fittings, connectors plus welding and cutting equipment.
New REGO-FIX Tool Holding, Metrology Innovations to Debut at IMTS
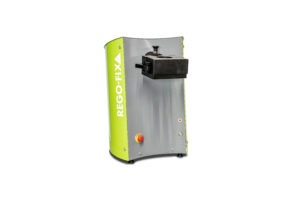
True to its legacy of Swiss precision and constant innovation, REGO-FIX USA (Whitestown, IN) will spotlight two new tool clamping/unclamping units for the company’s powRgrip® tool holding system and a new spindle drawbar force testing tool in Booth W-431822. The new units are the PGA (automatic) 9500 and the powRgrip Single, while the ForceMaster tool is the latest addition to the company’s family of metrology products.
The automation-ready PGA 9500 provides a simple way to automate the tool setup process when using the popular REGO-FIX powRgrip tool holding system. As such, it allows tools to be set up unmanned and around-the-clock. For seamless integration, it easily connects, via a robot, to other equipment as well as to tool storage areas. Its automatic door and easily controllable clamping device make the PGA 9500 well suited for working within existing automation systems. Its space-saving design, safe operation and the fact that it generates no heat or hazardous fumes make the clamping unit the ideal solution even in limited spaces.
The powRgrip Single, like the other members of the powRgrip family of tool holding systems, is easy to use and provides fast, efficient and safe operation. In fact, the powRgrip Single is the company’s fastest powRgrip clamping device with a cycle time of less than five seconds. It’s also smaller in size and manufactured with Swiss precision that ensures strong and stable gripping for longer tool life and cost effectiveness.
While existing powRgrip loading/unloading units accommodate several tool holding collet sizes, the powRgrip Single is designed for one holder size series. This is in direct response to shops requiring the use of only one series of PG holders.
To make machine tool spindle drawbar testing, tracking and documenting easier than ever, especially for shops with a variety of machines, REGO-FIX developed its ForceMaster drawbar tool. It allows shops to quickly measure drawbar pull-force, and the tool adapts to virtually any machine tool spindle. More than a dozen available adapters thread on to the tool to measure all popular spindle tapers, including HSK, SK, BT, CAT and others. This flexibility makes the ForceMaster a universal metrology tool for the shop floor.
Workholding Company Debuts Three new Products
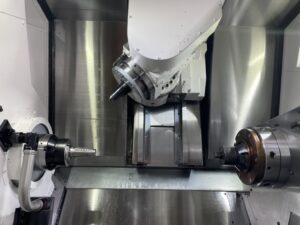
Continuing its 77-year tradition of master craftsmanship in providing high-quality clamping and gripping technologies for the manufacturing industry, Speedgrip Chuck Co. (Elkhart, IN), announced the availability of three new products. The company’s new products, the NDS Quick-Change Mandrel, QCR Quick-Change Receiver and CSC Contactless Stroke Control, improve productivity by making machine workholding changeovers faster and more reliable. Visitors can see these products firsthand in Booth W-432268.
“Our new products build on Speedgrip’s heritage and expertise as a leading innovator and producer of standard and customized workholding solutions for the full range of machining applications,” said Speedgrip’s President Matthew Mayer. “At the same time, they integrate new concepts and technology that keep pace with advanced manufacturing, automation and Industry 4.0.”
Among the three products is the versatile and efficient NDS Quick-Change Mandrel, which uses a unique rear bayonet mount that pulls and secures the workholding collet from behind, eliminating the need for draw screws. The no-draw-screw (NDS) configuration improves workpiece accessibility to quickly and efficiently combine outer diameter (OD) and inner diameter (ID) turning, facing and grinding into one operation with minimal interference.
Speedgrip’s patented one-piece sealed collet design outperforms the competition and does not break down with extended use under harsh machining coolants. As the most advanced workholding solution currently available, the NDS Quick-Change Mandrel allows for faster spindle speeds without loss of gripping power due to centrifugal force while significantly extending durability and service life. It is highly adjustable with steering screws to compensate for total indicated runout and concentricity, providing repeatable accuracy to 0.0003 of an inch. The unit is available in seven standard sizes ranging from 0.5”-to-5” for all standard spindle nose configurations and custom sizes are available upon request.
Each of Speedgrip’s new products are American made, in stock for fast delivery and backed by decades of workholding solution expertise.