Why High-quality Boring Tools Should be a Priority for Any Manufacturing Operation
A specialized or premium boring head can deliver a return on investment in a single production run.
Posted: August 2, 2024
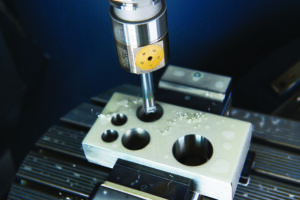
Picture two turbine discs, one machined by Shop A, the other by Shop B. At first glance, you’d think the two are identical. And yet, it’s hard to see the full story based on the shipped parts. Behind the scenes, Shop A dealt with several issues to get to the finished product: long cycle times, inconsistent bore quality, reduced tool life and scrapped parts. Shop B’s production, on the other hand, ran smoothly, and it delivered profitably on the job. So, what happened?
In many boring operations, it boils down to tool quality. Shop B utilized premium quality boring tools tailored to its needs (while Shop A cut corners). It’s an unfortunate but highly avoidable situation. Overcoming boring challenges starts with understanding some fundamental misconceptions about boring tools.
Common Misconceptions About Boring Tools
Even industry veterans fall prey to the following three misconceptions:
- “A boring tool is a boring tool is a boring tool.”
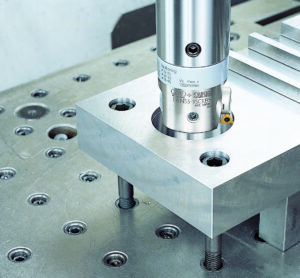
There’s a logic to this misconception. While designs and configurations may vary, most boring tools operate off the same general principles. But premium tool suppliers will deliver much more bang for your boring buck. For example, the Series 319 SW twin cutter boring heads offered by BIG DAISHOWA have a unique design feature that allows for balanced or stepped cutting without additional accessories or adjustments — simply by switching the mounting locations of the insert holders that have varying heights. This is a productivity game-change in rough boring. Meanwhile, some precision boring heads offer self-balancing capabilities, which significantly boost accuracy even at high power. Finally, premium boring partners will have options to meet challenging jobs such as ma on the market, for example. It all adds up to higher productivity and better profitability.
- “No need to go digital.”
Digital boring technology is a proven game-changer for many operations, but many shops still rely on older equipment. A good manual boring head can last quite a while, so some operators see no need to upgrade. But as a new generation of workers less experienced with manual calibration enters the industry, margins grow narrower, production schedules get shorter, and tolerances grow tighter. Spending half an hour making manual adjustments doesn’t make much sense. A digital head, on the other hand, is a bigger upfront investment, but can make adjustments of 50 millionths of an inch and eliminate human error (more on that later).
- “Boring tools shouldn’t cost that much!”
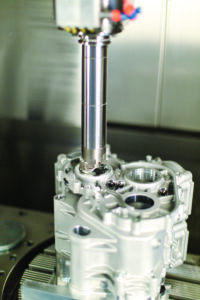
Speaking of cost, sticker shock is a real issue. Some tools simply cost more than others and it’s tempting to think to yourself, “I can get by with cheaper equipment.” But cutting costs at the start leads to more money spent down the line. Some shop owners, trying to pad margins, go with cheaper tooling, only to see it break down, damage multiple runs or worse. When you buy premium boring tools, on the other hand, you’re paying for design innovation and added features that pay you back in the long term. A few examples:
- Selecting the correct insert and cutting parameters is essential for process control. This helps reduce or even eliminate additional operations, which can create high labor costs.
- Digital boring heads are an investment, but they deliver higher accuracy with ease of adjustment while promoting operator confidence. In addition, they provide process control by tracking insert wear.
- Tools that provide a dual function may cost more but deliver twice as much. For example, twin boring tools provide the flexibility of both balance cutting at high feed rates or step cutting, which allows one to double the stock removal at half the feed rate when compared to balance cutting.
Big Boring Benefits
Contrary to the previously mentioned misconceptions, high-quality, innovation-driven boring tools can make all the difference for a shop’s bottom line. Let’s explore how.
- Maximum precision
Premium boring tools are extremely precise — which can have benefits even if you’re not dealing in microns. For example, boring tools designed with precision in mind can help reduce operator error. While most boring tool manufacturers produce only a metric version of their tool, every BIG DAISHOWA boring tool is available in both metric and inch systems. This eliminates the need for operators to convert to inches — which can result in a slight error with every adjustment (sometimes several microns). In many applications, this compromises the quality of the finished piece.
Digitization is another way premium boring heads are upping the ante. Digital boring heads help ensure the first diameter correction is exactly what’s required from the first hole measurement — showing diametric changes down to .00005”. This helps reduce human error and offers a high return on investment in a fairly short period of time.
- Consistency and repeatability
Just as important as precision, high-quality boring tools deliver more consistent, repeatable results, even in high-speed, challenging boring applications. The aforementioned self-balancing boring heads, for example, can deliver repeatable performance at high cutting speeds and feeds on small diameter bores due to an integrated counterweight, which allows for precision balancing of the tool assembly. This provides a more reliable operation and improvements to bore quality, surface finish and tool life.
And don’t forget the tool holder — worn or lower quality tool holders can lead to non-repeatable hole sizes because they affect how reliably and repeatably the tooling is being placed in the tool holder.
Finally, if you’re having repeatability issues with hole-roundness, premium tooling can help here, too. Twin cutting boring heads during roughing, for example, deliver opposing cutting forces that guarantee a round hole — setting the stage for positional accuracy and optimal finish boring.
- Long tool life
Speaking of breakage, it’s easy to forget just how much stress everyday operations place on your boring tools. Even the best, most durable tools out there eventually wear down. But choosing premium tools ideally suited for your application can help. When it comes to boring tools, one way to extend life is to focus on optimizing your rough boring — an operation that tends to eat through inserts quickly. The best way to do that is to use more of a plunging motion as opposed to interpolation, by way of a twin cutter boring head. It balances the load better, requires fewer inserts overall and ultimately helps with hole quality.
- Predictable downtime with digital
“Time is money” applies in many settings, but especially on a busy shop floor. Unplanned stoppage for adjusting bore sizes can be both frustrating and costly. Fortunately, digital tools offer a heads-up in the form of “predictive insert wear.” Monitoring the last 200 adjustments made allows one to become more predictive in controlling bore size instead of being reactive when the bore becomes undersize. The boring head maintains a log of compensation (insert wear) adjustments made in a register. By seeing a trend, operators can then plan maintenance ahead of time. Not only does this protect productivity, but it can also make for a more organized and lean shop floor — thanks to a just-in-time approach to tooling inventory management.
- Better return on investment
As stated above, shop owners shouldn’t look only at the price tag on tooling, particularly when the parts they produce are high-ticket or in high volume. Think about boring heads again. A specialized or premium boring head — when applied with expertise to the right operation — can deliver a return on investment in a single production run. Trying to make do with standard boring heads for challenging operations, on the other hand, will cost more than the upfront savings in the long run.