Additive Manufacturing Systems
Filter by Process Zone:
ASTM Releases R&D ‘Roadmap’
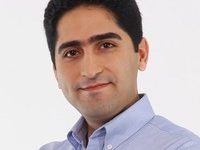
The document articulates upcoming AM standards, how to participate in AM R&D for standardization, and how the AM CoE is supporting industry needs by filling standard gaps. Mahdi Jamshidinia, Additive Manufacturing R&D project manager, says the roadmap provides a vision for the future of AM research and development.
Sandvik Plant Achieves Aerospace Certification

The company’s Sweden-based powder plant – which produces its Osprey titanium powder and nickel-based superalloys used for additive manufacturing – has received AS9100D certification. Meeting the high standards for the aerospace industry with meticulous attention to weight, traceability, consistency and more, the facility is accelerating adoption of 3D printed titanium parts and shifting toward sustainable manufacturing.
Mark Your Calendar for Virtual Workshop April 22: Certification, Standardization in AM Adoption

ASTM’s Additive Manufacturing Center of Excellence will host a program filled with technical talks and panel discussions focused on technology adoption through standardization and certification. Recognizing current gaps to meet the needs of industries like aerospace, medical, and automotive, ASTM and its German testing/certification partner are making the workshop open to all AM professionals.
Quality and Reverse-Engineering Tips During Social Distancing
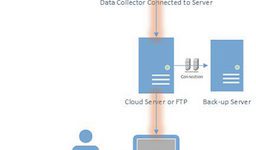
Exact Metrology offers practical ways to maintain safe, effective production in the workplace. Maintaining a six-foot distance from others as well as frequent hand-washing and device sanitizing are critical.
3D Printing Dashboard Empowers Production Manager, Runs on Most Brands
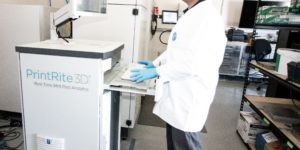
As 3D printing of metal parts increases, Sigma Labs launches PrintRite3D Production Series to speed up design, development and execution during the present worldwide virus crisis. Its Production Dashboard and AI-driven metrics provide real-time, actionable information during the production process.
Long-Distance Weld Purge Monitoring

Huntingdon Fusion Techniques HF’s PurgEye 1000 measures 1 ppm to 1,000 ppm of oxygen from up to 1 kilometer away. Integrated networking device can share the reading from the monitor with another piece of equipment, such as a visual warning accessory or dew point monitor.
Save Time and Money with Inflatable Purging System

PurgElite from Huntingdon Fusion Techniques HFT tube and pipe purging systems help welders quickly achieve a clean, oxide-free, zero-color weld. Manufactured for diameters from 1 in to 24 in (25 mm to 600 mm), their integral gas feed device eliminates complicated valving for the operator to adjust and set.
Inert Gas Feed Hoses for a Variety of Applications

Off-the-shelf inert gas feed hoses from Huntingdon Fusion Techniques HFT ensure argon, helium, and other gas arrives uncontaminated. The hoses can also be supplied to all other TIG/GTAW welders as well as laser operators with their own special fittings as required.
Laser Deposition Welding Combined with 5-Axis Milling for Large Parts

A new machine size in powder nozzle technology, DMG MORI’s Lasertec 3D hybrid is designed for the additive manufacture of complex prototypes and small series parts as well as component repair and coating. It enables additive manufacturing and CNC milling on one machine – for 3D components in finished part quality.
Laser Deposition Head Optimizes DED Processing
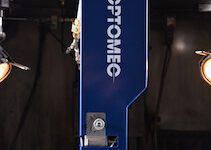
Optomec’s LENS LDH 3.X brings the flexibility and versatility to build, repair, coat, and clad parts into one deposition head. Variable optics system that creates three focused spot sizes optimizes directed energy deposition (DED) processing across a range of parts and applications.
3D Metal Printer Is 40% Faster Than Predecessor
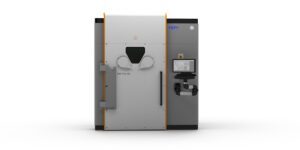
The DMP Flex 350 from GF Machining Solutions is the successor to 3D Systems’ ProX DMP 320 3D metal printer. Consistent repeatability is achieved with its pure, low-oxygen environment during printing.
Sustainably Sourced Metal Powders for Additive Manufacturing

6K’s UniMelt microwave plasma platform converts recycled material into premium powder. The technology processes almost any metal type, alloy, or ceramic feedstock, which means any alloy that’s machined has the potential to become powder.