Filler Metals/Electrodes
Filter by Process Zone:
Metal-Cored Wires Remain Strong After Extensive Stress Relief

FabCOR 4130 SR and SubCOR 4130 SR wires from Hobart are ideal for single and multi-pass welding in oil and gas and offshore applications, wellhead fabrication and repair, and others using high-strength low-alloy steels.
Flux-Cored Wire Offers Low Hydrogen (H4) Weld Deposits, Superior “As-Welded” and PWHT Properties

FabCO 712M gas-shielded flux-cored wire from Hobart Brothers is ideal for offshore drilling rig applications and jack-up rig fabrication.
Understanding the Basics of Low-Hydrogen Stick Electrodes

Knowing the basics about E7018 low-hydrogen stick electrodes can be helpful in understanding how to maximize their operation, their performance and the welds they can produce.
Hobart Campaign Celebrates Partnership with U.S. Navy
The campaign, “It’s the tie that binds,” showcases the Marine Group Boat Works partnership with the U.S. Navy to celebrate creating some of the most distinctive and instrumental things that impact the world.
Hobart Launches New Brand Campaign
“It’s the tie that binds” celebrates the journey from the filler metals customers use to the relationships developed on the journey to find the right filler metal solution.
Metal-Cored Wire Offers Higher Deposition Rates, Faster Travel Speeds to Increase Productivity

FabCOR® F6 wire from Hobart Brothers provides higher deposition rates and faster travel speeds to help increase productivity on single-pass, flat and horizontal welding applications, with deposition efficiencies similar to solid wire but with reduced spatter to minimize clean up.
Flux-Cored Wires Offer Lowest Manganese Levels in the Marketplace
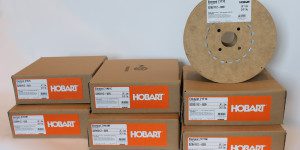
Through the the innovative formulation of the flux fill, Element™ wires from Hobart Brothers produce manganese emissions well below the levels of other gas-shielded flux-cored wires without sacrificing mechanical properties or weldability. They provide very low spatter levels and consistent arc stability that ensures reliable welding performance on a variety of applications.
Understanding the Basics of Flux-Cored Wires

As with any filler metal, welders must weigh out the advantages and disadvantages of gas-shielded and self-shielded FCAW wires to determine if these are the best choice for their specific application.
Aluminum Filler Metals Approved for Wrought Commercial Applications

Maxal offers patent-pending 4943 aluminum MIG wire and TIG cut-lengths for a higher-strength aluminum welding solution that also offers the advantages of using a 4043 aluminum filler metal, including excellent corrosion resistance, ease of welding and low hot cracking sensitivity. It is also suitable for elevated temperature applications, and provides the ability to reduce weld size without compromising strength.
New Product Catalogs On Filler Metal Solutions

One new Hobart® catalog includes products currently branded as Tri-Mark® by Hobart, alongside Hobart products. The catalog also features aluminum products formerly branded as MAXAL®. The other new catalog is the McKay® by Hobartcatalog, which features stainless steel and hardfacing wires.
Stick Welding Still Has a Place in the Fabrication Industry

Many applications in the fabrication industry still require stick welding. Like other filler metals, stick electrodes are available in many types, each of which provide different mechanical properties and operate with a specific type of welding power source. Before you power up your machine and pick up your stick electrode holder, consider these basic guidelines to help simplify your stick welding experience.
Characteristics of Heat Treatable vs. Non Heat Treatable Aluminum Alloys

There are certainly differences in strengths for aluminum alloys, whether they are heat-treatable or not. These different characteristics impact the final strength of the weld because these alloys differ in their chemical and metallurgical structure and in how they react during the welding process.