Filler Metals/Electrodes
Filter by Process Zone:
FABTECH 2016 Sneak Preview: Welding

The 2016 edition of FABTECH is on track to be one of the largest metal fabrication events ever at the Las Vegas Convention Center in Las Vegas from November 16-18. This special sneak peek provides technical reviews of some of the equipment, power sources, positioners, systems and accessories that will be exhibited in the Welding Pavilion to help you get a head start on navigating the show floor and managing your time while you’re there.
Filler Metals Address Welding Challenges

Filler metal solutions from Hobart Brothers improve productivity, quality and cost savings in metal fabrication and manufacturing applications.
How to Get More Weld Strength in Powerboat Propulsion Systems

Nothing pushes the limits of machine performance – or weld strength – like offshore powerboat racing. To meet its demands of higher strength, corrosion resistance, ease of welding and low hot cracking sensitivity, this powerboat drive builder uses an advanced aluminum filler metal that significantly strengthens weld joints after post-weld heat treatment and machining, without affecting the integrity of the base metals.
Tube & Pipe Fabrication: Welding

Here are some of the advances in tube and pipe welding equipment and accessories that are now available to help shops make money while meeting demands for more complex geometries, tougher materials, faster speed and higher quality.
Low Hydrogen Weld Deposit, Minimal Cracking Risks When Welding Pipe

FabCO 750M gas-shielded flux-cored wire from Hobart provides low diffusible hydrogen weld deposits on high-strength applications and minimizes the risk of underbead cracking.
Pure DC Generator Power Source for Pipeline Applications

The engine-driven SAE-300 MP Pure DC Generator Welder from Lincoln Electric stands up to rough conditions on the job site and delivers consistent power and maximum control, no matter how hot or cold, how long the pipeline or how tough the job.
Welding Abrasion-Resistant Plate: Three Common Challenges and Their Solutions

Here are some tips that make it easier to avoid cracks and prevent lost time and money when welding these incredibly hard plates.
The Importance of Proper Welding Operator Training

To gain more business in the face of a skilled labor shortage, fabrication shops need welding operators that are familiar with a wider variety of welding processes and materials and can take on new jobs to set their shops apart. Proper operator training plays a key role in reaching these goals.
New Welding Wire Withstands Extreme Heat Conditions

Costing about 50 percent less than comparable cobalt materials, 5551 flux-cored wire from Weld Mold retains superior hardness in temperatures up to 1,200 deg F.
New Wire Offers Higher Deposition Rates and Travel Speeds for Welding Heavy Equipment

Ideal for heavy equipment welding and for equipment used in severe service conditions, the new FabCO 85HXP gas-shielded flux-cored wire from Hobart Brothers can operate at higher wire feed speeds to increase deposition rates and travel speeds on thicker materials for higher productivity.
Increasing Aluminum Weld Strength and Quality

Aluminum is popular in many fabrication applications, but welding the material presents challenges of cracking, porosity and burn-through on thinner sections. Here are some critical insights on how to combat these potential problems.
Weathering Steel: Taking the Guesswork Out of Filler Metal Selection
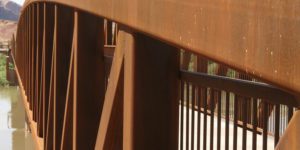
Weathering steel offers excellent resistance to atmospheric corrosion caused by rain, snow or humidity. During the welding process, the filler metal type and the manner in which it is applied determines whether the resulting weld will match corrosion resistance or have the same reddish appearance, more commonly known as color match.