Filler Metals/Electrodes
Filter by Process Zone:
Gas-Shielded Flux-Cored Wires Lower Manganese Emissions Even More

FabCO Element 71C and 71M wires from Hobart are ideal for welding in shipbuilding, structural steel, heavy equipment manufacturing and general fabrication.
Consumables for Harsh Industrial Work

Stoody nickel-based tungsten carbide consumables from ESAB offer a wide range of tailored hardfacing and high alloy joining solutions to address wear caused by abrasion, impact, corrosion and heat.
Premium Feeding for Construction and Field Welding
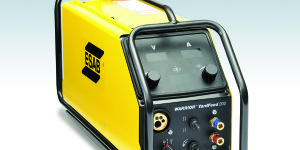
These advanced wire feeders from ESAB are ideal for ship/barge, off-shore and construction applications where operators change welding parameters, use hotter settings for welding in the flat position and cooler settings for welding vertical up.
Submerged Arc Welding Flux for Chrome-Moly Steels

The SWX 160 flux from Hobart helps meet X-factor requirements, along with providing excellent impact toughness to further ensure weld performance in high-strength applications.
Considerations When Selecting a Filler Metal (Part Two)

Although the effect of various elements in filler metals can be rather complex, a review of their general properties can also help welding operators determine which filler metal is ideal for the job. It is important to consider the properties needed in a completed weld when making the filler metal selection.
Down to the (Flux-Cored) Wire
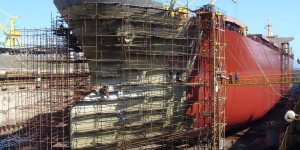
Designed specifically for toughness in critical applications, these new flux-cored wire solutions meet the most unforgiving demands of shipbuilding and offshore fabrication.
Ways to Get the Most Out of Your MIG Gun Consumables
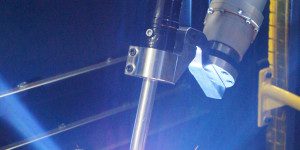
Here are a few of the best practices that every welding operator should know when it comes to choosing and maintaining nozzles, contact tips, retaining heads and gas diffusers, and cable.
Mild Steel and Low-Alloy Flux-Cored Welding Wires
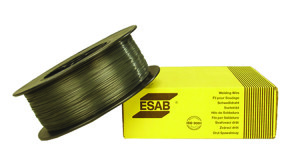
ESAB offers two wires in its series of flux-cored welding consumables: Dual Shield II 4130 SR and Dual Shield II 70-Ni1 H4.
Tough Flux-Cored Wire for Shipbuilding and Demanding Offshore Work

Premium UltraCore gas-shielded flux-cored wire from Lincoln Electric creates a tough weld that stands up to temperature extremes, corrosive saltwater, constant moisture and other adverse conditions, while exceeding demanding industry requirements.
Excellent Low-Temperature Toughness for Critical Applications

The new FabCO 812-Ni1M wire from Hobart Brothers has been formulated to provide excellent low-temperature impact toughness for critical applications.
Matching Filler Metals to Stainless Steels

Welding stainless remains complicated. Besides paying close attention to heating and cooling the stainless, the filler metal must be properly matched to the base metal with electrodes of the same grade.
Considerations When Selecting a Filler Metal (Part One)

Filler metal selection is critical to maintain the integrity of the final weldment. Here is a review of their general properties that can help you determine which filler metal is ideal for the job.