Milling Machines
Filter by Process Zone:
When Bigger Really is Better

This machine shop took an unconventional approach to growing into one of the most dependable parts suppliers for a major manufacturer of construction and mining equipment, and now they enjoy a niche that most shops are unable to compete against.
High Precision Machining, Lower Cost Metal 3D Hybrid Machining of Large Parts
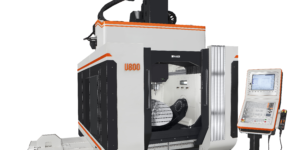
Large scale machining centers from Takumi USA are integrated with Metal 3D Printing Tools from 3D-Hybrid Solutions to break new ground in aerospace, tooling, mold and die applications.
Bridge-Type Machining for Mold and Aerospace Precision
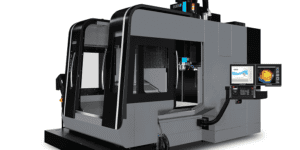
With the spindle center line being closer to the supporting structure, the dual column bridge-type BX50i from Hurco minimizes machine distortion and thermal deformation and increases rigidity with maximum support to the head casting.
Bridge Mills for High Speed Machining of Large Parts at a Reduced Cost
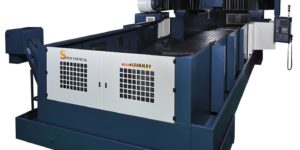
The long base casting of Johnford DMC LH Series double-column moving table bridge mills from Absolute Machine Tools provides complete support of the table over the full X-axis travel so that massive loads can be machined.
Innovative Manufacturing for the Factory of the Future

A wide range of high speed milling, EDM, laser texturing, additive manufacturing, micromachining, automation, tooling and connectivity systems from GF Machining Solutions are designed for manufacturing automotive, aerospace, medical, information and communications technology, electrical components, and mold and die components.
Seco Machine Announces Plans for New Plant
This larger $8 million plant will meet growing demand for their contract machining services and custom-molded urethane parts.
Plug-and-Play Robotic Manufacturing Cells Increase Productivity, Lower Costs
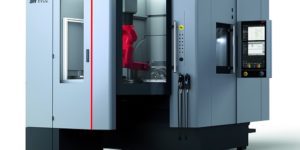
Dual-spindle BA 222 or BA WO2-22 machining centers integrated with a 6-axis robot from SW North America provide high speed machining of complex parts made of non-magnetic materials, watchmaking components, automotive impellers and other precision engineering work.
High Speed Milling with Intuitive Touch-Screen Machine Control for Ultrafast Setup
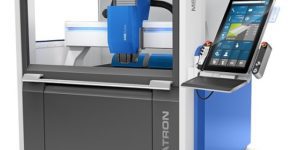
The M8Cube Next high speed milling machine from DATRON Dynamics is ideal for precision, high or low volume production of electronic, aerospace and medical parts, as well as industrial engraving applications.
GFMS Expands Territory of Applied Machine Solutions
AMSI is now their exclusive distributor and representative in Georgia and Alabama, as well as Florida.
ATEK Expands Northeastern Iowa Plant
As part of the expansion, they are improving their plant automation program with a major investment in robotic de-gating and deburring of castings.
Advanced Precision Machining of Complex Aerospace Components
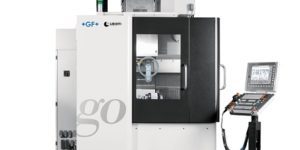
The 5-axis Liechti go-Mill 350, Mikron MILL P 800 U ST and FORM 200 die-sinking EDM from GF Machining Solutions generate flawless surface finishes on complex part shapes found in turbines and cell components for avionics.
Take 5-Axis Machining of Aerospace Parts to the Next Level
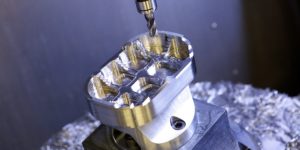
Machining aerospace components involves very long cycle times and often high raw material costs that present competitive challenges for OEMs and production job shops alike. But here are two examples of how the latest CAD-CAM-CNC workflow can improve design-to-part protocols, machining time, tool life, surface finish, dimensional accuracies and overall production efficiencies.