Wire Feeders
Filter by Process Zone:
Systems for Medium- and Heavy-Duty Industrial Welding
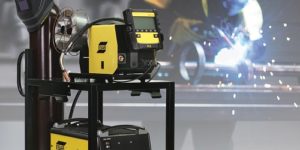
Aristo industrial welding systems from ESAB combine new and improved components in 21 ready-to-weld packages that increase quality and lower the cost of operation in welding aluminum, stainless and carbon steel.
New Lincoln Electric Welding Technology & Training Center to Open in January 2018

This 100,000+ sq ft building doubles their welding education capacity and will be one of the most advanced facilities of its kind.
Innovative Automated Technology Increases Efficiency in Aluminum Welding

Ideal for manufacturers of trains, road tankers and chemical tanks, shipbuilding and aerospace components, the ARCLINE PP automated welding process from Linde Gases features a positively energized tungsten electrode for constant cathodic cleaning of the welding area to reduce the risk of inclusions and minimize the need for pre-weld cleaning.
Field vs. Shop: What’s the Best Welding Process for Structural Steel Fabrication?

Whether structural steel welding is taking place in an indoor shop setting or outdoors in the field is a factor that either introduces or eliminates a host of elements, including wind, the enemy of shielding gas and the welding processes that rely on it. Here are some insights to help you choose the right structural steel fabrication process for a field application or for shop welding.
Lincoln Electric Partners with SmartEquip Network
SmartEquip now provides owners of Lincoln Electric welding equipment with product information and parts support catalogs to maintain their fleet.
Tips for Successful Aluminum MIG Welding Repairs

With its low melting point, the presence of an oxide layer on its surface, prone to burn-through with a difficult-to-control weld pool, aluminum can be somewhat tricky. Here are some insights that will provide you with the best course of action to take for making a repair.
Miller Electric and Hobart Brothers Earn Stringent Quality Certification
Both companies are registered to ISO 9001:2015 for sharing organizational knowledge, risk assessment, top management leadership and improvements.
Avoid These Costly Mistakes in the Welding Operation

Looking to improve productivity and reduce costs to be more competitive? The one key to getting ahead is reducing the time spent on non-value-added activities – i.e., any time spent not welding. Here are some of the best ways to reduce downtime.
Miller Electric Celebrates Welders and Why They Build
Their “#whyiweldcontest” giveaway recognizes enthusiastic welders and celebrates the things that inspire them.
IWDC Spending Sets New Record
The spending of Independent Welding Distributors Cooperative member companies through their co-op exceeded $19 million in March.
Choosing the Right Drive Roll is Key for Smooth Wire Feeding
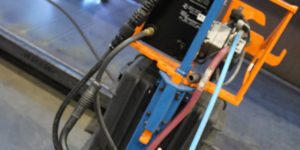
Is your wire welding operation being challenged by poor feedability, birdnesting, burnback, or clogging of the gun liner? If so, you may be using the wrong type or size of drive rolls for the job, or using improper drive roll tension. Here are some tips to help you prevent downtime and its associated costs due to poor wire feeding.
Let It Flow: Tube & Pipe Welding

As business picks up for tube and pipe fabricators, they must reduce their setup times and become more versatile in the flow of work they are able to handle, all while increasing their productivity to remain competitive. Here is some of the latest tube and pipe fabrication and welding equipment that can help these shops smooth out jobs so that their work goes with the flow.