Column
Filter by Process Zone:
A5.36 Filler Metal Specification: What Does It Mean to You?
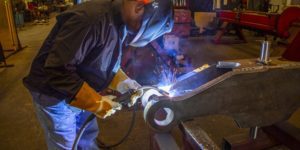
This new open classification combines four other AWS specifications and is one that is garnering some questions. Let’s take a closer look at why it was developed and how it applies to your welding operations.
Robotic Simulation to Bridge the Skills Gap

Because robots still only do what they are programmed to do and still require qualified personnel to build, operate and maintain them, savvy shops realize that creating a workforce skilled in Industry 4.0 technologies is key to future competitiveness – but certain challenges make this difficult. What should they do?
Three Trends to Watch in Metalworking

Take a closer look at some of the steps that shops are taking to remain competitive in an increasingly high-tech, globalized industry; what obstacles they’re facing; and how they’re using technology to work smarter, better, and faster.
How to Defeat Downtime

No one is happy when a machine goes down because of tooling issues – wasted time that is even more frustrating when it’s avoidable. Arrow Storage Products found a way to significantly reduce their machine downtime and cut their average tooling downtime per week due to tooling by 70 percent.
Fabricating and Repairing 4130 and 4140 Steels in Heavy Equipment Welding
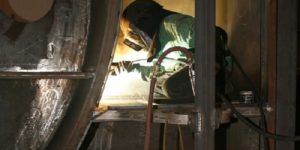
The strength of these steels is great for parts that require high strength and durability, but their higher carbon, chromium and molybdenum levels also make them more susceptible to cracking. Here are some insights into welding these steels during new fabrication and in repair, and how the right filler metal can help ensure success.
Keeping it Cool: Why Machines Depend on Chillers, and Chillers Depend on You
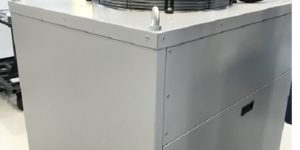
Lax water maintenance has a huge potential downside in laser cutting machines: bad water could lead to extreme overheating and complete failure of the laser. Here are some other reasons why keeping cool and remembering to change the chiller water will get the most work out of your machinery at the lowest cost of ownership.
Connective Forms Make Fastening Faster

Incorporating connective forms into your existing fabrication assembly process adds functionality to sheet metal components in the place of conventional fastening methods. Available for most styles of punch press, connective forming tools remove secondary welding, fasting and clipping operations to reduce assembly time and produce valuable cost savings.
How Proprietary Grains Optimize Non-Woven Abrasives for Superb Finishes

Take a closer look at how a Midwest appliance manufacturer used non-woven agglomerated grain technology to put a structured cosmetic finish on a ring for a high-end kitchen appliance, remove the medium-sized burrs left on the ring from stamping, and increase their productivity by 5X!
Building a Robotic Workcell Champion
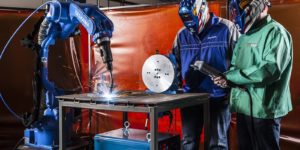
How do the most productive and efficient shops achieve faster ROI and rationalize more cell purchases? Many have a trained champion who garners support from other team members to meet deadlines and becomes accountable for the new or existing robotic workcell.
How to Prevent Five Common Failures in Robotic Welding Systems
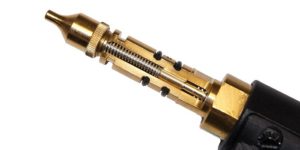
Are burnbacks, premature contact tip wear, loss of tool center point (TCP) or other problems costing your robotic welding operation time and money? Here are some tips that will improve productivity, reduce consumable costs and ensure consistent part quality in your robotic weld cell.
How to Avoid Losing Customers to Competitors
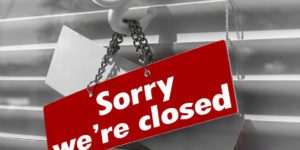
What’s the best strategy for keeping encroaching competitors away from your customers?
Critical Thinking: How to Make Chip Removal More Efficient, Effective and Profitable
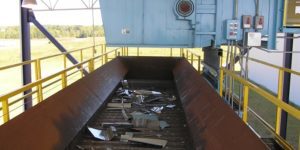
Not all conveying systems are suited for every scrap-handling application. By using the proper conveyor to quickly transfer scrap and coolant from the machine tool for separation and processing, high volume machine shops can increase part production with less downtime between jobs, create more value for their scrap, and improve revenue by recycling coolant.